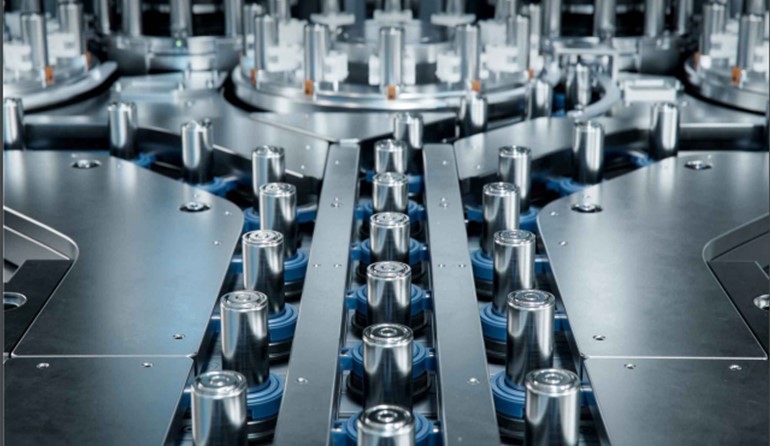
آینده کارخانه سلول باتری
مقدمه
تقاضای جهانی برای باتری در حال افزایش است، اما نه به آن سرعتی که کارشناسان بازار پیش بینی میکردند. در نتیجه، ظرفیت تولید سلول جهانی اعلام شده میتواند تا دو برابر تقاضا را در طول پنج سال آینده بیشتر کند که عمدتاً ناشی از تولید بیش از حد در چین است. ظرفیت مازاد و نرخ بهرهبرداری پایین باعث رقابت شدید قیمتها، بهویژه از سوی تولیدکنندگان آسیایی ارزانقیمت میشود و کارایی عملیاتی را برای حفظ رقابت ضروری میسازد. در مقاله ای قبلا به چالشهای شرکتهای تولید کنندگان اروپایی پرداخته شده است.
برای بهینهسازی کارایی، تولیدکنندگان سلول میتوانند کارخانه به انواع بهینه شده آینده ارتقا پیدا کنند و به طور بالقوه هزینههای تبدیل را تا 30% کاهش دهند. این دگرگونی شامل مقاوم سازی کارخانه های موجود و طراحی امکانات جدید است که فناوری های پیشرو را مانند آخرین پیشرفت ها در اتوماسیون و هوش مصنوعی، همراه با بهبود فرآیند ناب اثبات شده در بر می گیرد.
سازندگان سلول باید هزینه های تبدیل را کاهش دهند
تولیدکنندگان در تلاشهای خود برای افزایش کارایی، همزمان باید کاهش هزینههای تبدیل - یعنی هزینههای تولید بدون احتساب هزینههای مواد که 20 تا 30 درصد از کل هزینههای تولید باتری را تشکیل میدهند، در اولویت قرار دهند. شکل 1 دو روند قابل توجه را برجسته می کند. اول، با کاهش هزینه های مواد، هزینه های تبدیل قابل توجه تر می شود. هزینه های تبدیل حدود 20% از هزینه های تولید باتری های نیکل منگنز کبالت (NMC) در مقابل تقریباً 30% برای باتری های لیتیوم آهن فسفات (LFP) را تشکیل می دهد. دوم، ماهیت بسیار هزینه بر تولید باتری، با استهلاک تجهیزات که به طور قابل توجهی در هزینه های تبدیل نقش دارد، بر اهمیت حداکثر کردن کارایی کارخانه تاکید می کند.
|
شکل1: هزینه های تبدیل با کاهش هزینه های مواد معنادار |
نکته دیگر که باعث تفاوت هزینه تولید می شود، تفاوتهای منطقهای در هزینههای آب و برق و نیروی کار، ضرورت بیشتری برای پرداختن به تشدید رقابت جهانی هزینه ها ایجاد میکند. هزینههای پایینتر آب و برق و نیروی کار در چین منجر شده است که هزینههای تبدیل باتریهای کیسهای NMC تقریباً 13 دلار در هر کیلووات ساعت (کیلووات ساعت) شود، در مقایسه در ایالات متحده با 17 دلار در هر کیلووات ساعت و 22 دلار در هر کیلووات ساعت در آلمان (شکل 2) تولید می شود.
|
شکل2: ساختار هزینه بر اساس کشورهای متفاوت |
کارخانه سلول باتری در آینده راه حلهایی را ارائه می دهد
کارخانه سلول باتری در آینده به چالشهای بهینه سازی هزینه از طریق بهبود در چهار بعد رسیدگی می کند. هر بعد شامل انواع معیارهای نوآورانه است که سطوح مختلف بلوغ فناوری را در بر می گیرد.
سطوح بلوغ فناوری
اقدامات نوآورانه در کارخانه آینده در چهار مرحله مختلف بلوغ تکنولوژیکی قرار دارند:
- فاز تحقیق. مفاهیم جدید در یک محیط آزمایشگاهی کنترلشده آزمایش و پالایش میشوند تا امکانسنجی و مزایای بالقوه آنها تأیید شود.
- فاز آزمایشی. فنآوریها در یک خط تولید آزمایشی در مقیاس کوچک در یک محیط تولید واقعی آزمایش میشوند تا عملکرد، مقیاسپذیری و ادغام آنها با سیستمهای موجود ارزیابی شود.
- فاز Ramp-Up. تکنیک ها در مراحل افزایشی برای تولید در مقیاس بزرگ، با تمرکز بر عملیات مقیاس بندی، بهینه سازی فرآیندها و پرداختن به هر گونه چالش عملیاتی به کار گرفته میشوند.
- استقرار در مقیاس بزرگ. اقدامات به طور کامل در تولید انبوه ادغام شده است، با ظرفیت کامل با قابلیت اطمینان، کارایی و بلوغ اثبات شده کار می کند.
- ساختار
بهینه سازی طرحهای کارخانه و زیرساختهای خاص باتری می تواند هزینه های عملیاتی و ردپای فیزیکی را به میزان قابل توجهی کاهش دهد. اقدامات ارزشمند شامل موارد زیر است.
محیط های کوچک. راه اندازی کارخانه های رایج، معمولاً به اتاق های خشک یا تمیز بزرگ و پرهزینه متکی هستند که می تواند تا 30% از کل هزینه های آب و برق را تشکیل دهد. محیطهای کوچک با حفظ شرایط کنترلشده در اطراف تجهیزات خاص، جایگزین کارآمدتری را ارائه میدهند و به محیط اطراف اجازه میدهند در شرایط عادی کار کنند. این رویکرد هدفمند با به حداقل رساندن حجم هوایی که نیاز به مدیریت دارد، هزینه های عملیاتی را کاهش می دهد. با این حال، محیطهای کوچک پیچیدگیهای تعمیر و نگهداری را بیشتری دارند و یکپارچگی با سیستمهای اتوماسیون، مانند وسایل نقلیه هدایتشونده خودکار برای حمل و نقل مواد را ضروری میسازند. اگرچه اکنون محیط های کوچک برای پر کردن الکترولیت به کار گرفته شده است، این فناوری هنوز در مرحله آزمایشی است و استقرار در مقیاس بزرگ ثابت نشده است.
چیدمانهای چند طبقه. چیدمانهای چند طبقه می توانند ردپای محیطی یک کارخانه را کاهش دهند و در عین حال مسیرهای لجستیک داخل کارخانه را کوتاه کنند. از نمونه های قابل توجه می توان به تأسیسات تسلا در برلین و کارخانه انرژی ال جی در لهستان اشاره کرد. با این حال، مزایای این طرح باید به دقت در برابر چالشهایی که شامل محدودیتهای تحمل بار، افزایش ارتعاش و هزینههای ساخت بالاتر میشود، متعادل شود.
طراحی مدولار. طراحی مدولار یا جدا کردن مراحل تولید، مانند پوشش الکترود، خشک کردن، تقویم کردن و برش، انعطافپذیری کارخانه را افزایش میدهد. این اجازه را می دهد تا تغییرات به طور مستقل اجرا شود و در صورت نیاز جایگزینی تجهیزات تولید با ماشین آلات یا فناوریهای جدید را تسهیل می کند.
- فناوری
پیشرفت های تکنولوژیکی می تواند عملکرد را بهبود بخشد و در عین حال هزینه های آب و برق و نیروی کار را کاهش دهد. بیش از 30 نوآوری فناوری در شکل 4 ارزیابی شده است و آنها بر اساس بلوغ و تأثیر تجاری رتبه بندی شده اند. سه نمونه از اقدامات بسیار ارزشمند شامل موارد زیر است.
![]() |
شکل4: رتبه بندی نوآوری ها را بر اساس بلوغ و تأثیر کسب و کار |
اختلاط مداوم. میکسرهای سیاره ای دوگانه معمولی دوغاب را به صورت دستهای تولید می کنند. این فرآیند دارای معایبی است، از جمله نیاز به مخازن بافر و توقف ماشین برای حذف مواد، که باعث کاهش کارایی می شود. میکسرهای پیوسته با مخلوط کردن مواد در یک جریان ثابت با استفاده از یک اکسترودر، جایگزینی را ارائه می دهند. این رویکرد پتانسیل افزایش قابل توجهی را دارد - تا 3000 لیتر در ساعت در مقایسه با 1000 لیتر در ساعت معمولی مخلوط کردن دسته ای - در حالی که نیاز به ذخیره سازی بافر را از بین می برد. علاوه بر این، اکسترودرها توانایی ورز دادن مواد را دارند که فرآیندی حیاتی برای شکستن آگلومراهای پودری است. در تئوری، این اجازه میدهد تا میکسرهای اکستروژن به کیفیت دوغاب برتر از میکسرهای سنتی دست یابند.
با این حال، قبل از اینکه اختلاط مداوم از مرحله آزمایشی فعلی به پذیرش در مقیاس بزرگ تبدیل شود، باید چندین چالش حل شود. مهمتر از همه، اطمینان از جریان ثابت خوراک مواد پودری همچنان یک چالش است و برای حفظ قابلیت اطمینان به سیستم های کنترل کیفیت پیشرفته نیاز دارد.
خشک کردن مادون قرمز. اجاقهای همرفتی معمولی که برای خشک کردن الکترودها استفاده میشوند دارای چندین اشکال هستند، از جمله نگرانیهای ایمنی ناشی از نشت احتمالی در کورههای روغن داغ (با دمای 200 درجه سانتیگراد تا 300 درجه سانتیگراد کار میکنند)، زمان راهاندازی و خنککردن طولانی، و هزینههای بالای نگهداری. خشک کردن مادون قرمز یک جایگزین است، با استفاده از پنلهای تابشی مادون قرمز برای تبخیر سریع حلالها. این روش می تواند هم نیاز انرژی و هم فضای مورد نیاز را کاهش دهد. با این حال، کنترل دقیق چگالی انرژی برای جلوگیری از مسائلی مانند جداسازی بایندر یا در موارد شدید، احتراق با حلال بسیار مهم است. برای مقابله با این خطرات، برخی از تولیدکنندگان باتری، خشک کردن مادون قرمز را با اجاقهای همرفت ترکیب میکنند. در حالی که خشک کردن مادون قرمز به طور گسترده توسط فروشندگان تجهیزات در دسترس است، پذیرش آن توسط تولیدکنندگان باتری هنوز در مرحله افزایش است.
پوشش خشک الکترود. فرآیندهای معمولی پوشش مرطوب به حلالها برای کمک به مخلوط کردن ذرات ماده فعال و چسبنده متکی هستند. بخش قابل توجهی از مرحله خشک کردن بعدی به حذف این حلال ها اختصاص یافته است که به کوره های بزرگ و سیستم های بازیابی حلال نیاز دارد. پوشش خشک الکترود با مخلوط کردن مستقیم بایندر با پودر ماده فعال، نیاز به حلال را از بین می برد. این رویکرد مزایای قابل توجهی از جمله حذف کورهها و سیستمهای بازیابی حلال و همچنین افزایش بالقوه در بازده اختلاط تا 30 درصد به دلیل عدم وجود حلال را نوید میدهد.
پیشرفت های تکنولوژیکی می تواند عملکرد را بهبود بخشد و در عین حال هزینه های آب و برق و نیروی کار را کاهش دهد.
با توجه به پتانسیل آن، اکثر تولیدکنندگان باتری به طور فعال در حال توسعه این فناوری هستند و امکان سنجی آن را در خطوط آزمایشی نشان داده اند. به عنوان مثال، LG Energy Solution قصد دارد تا سال 2028 پوشش خشک را تجاری کند و تخمین می زند که می تواند هزینه های تولید را تا 19% کاهش دهد. با این حال، استفاده از این فناوری در عملیات در مقیاس بزرگ، به ویژه در سرعت پوشش 60 متر در دقیقه یا بالاتر، یک چالش مهم باقی مانده است. موانع کلیدی عبارتند از جلوگیری از سوراخ در لایه پودر، اطمینان از قوام لبه، و حفظ ضخامت یکنواخت فیلم. قابل توجه است که پوشش خشک کاتدی چالش های بزرگ تری نسبت به پوشش خشک آند ایجاد میکند. در نتیجه، قابلیت زنده ماندن این فناوری در مقیاس بزرگ هنوز مورد بحث است و در مرحله آزمایشی باقی می ماند.
- دیجیتال سازی و هوش مصنوعی
ابزارهای دیجیتال و آخرین پیشرفتهای هوش مصنوعی میتوانند زمان کارکرد دستگاه را افزایش داده و کار دستی را کاهش دهند. نمونه های برجسته شامل موارد زیر است.
سیستم دای اسلات خودکنترل. سیستمهای پوشش معمولی به تنظیمات دستی برای پارامترهای دوغاب مانند ضخامت، هر بار که یک کویل فویل جدید بارگذاری می شود، نیاز دارند. با کویلهای معمولی ۱۰ کیلومتر و سرعت پوششدهی به طور متوسط ۶۰ متر در دقیقه، این فرآیند تنظیم تقریباً هر سه ساعت یکبار مورد نیاز است، که اغلب ۱۵ تا ۲۰ متر فویل را در هر تنظیم هدر میدهد. سیستمهای دای اسلات خودکنترلی با یادگیری ماشینی این مشکل را برطرف میکنند و از ابزارهای اندازهگیری پیشرفته - مانند گیتهای بتا و سیستمهای بینایی - برای ارائه بازخورد بیدرنگ در مورد مشخصات و سازگاری لبه استفاده میکنند. این سیستم زاویه لبه و عرض جریان واحد پوشش را بهطور خودکار بر اساس داده ها تنظیم می کند، ضایعات فویل را کاهش می دهد و کارایی کلی روکش را بهبود می بخشد. این فناوری در حال حاضر در مرحله ارتقاء است.
ابزارهای دیجیتال و آخرین پیشرفتهای هوش مصنوعی میتوانند زمان کارکرد دستگاه را افزایش داده و کار انسانی را کاهش دهند.
پیری مبتنی بر شرایط. فرآیند پیری سلولهای باتری در پایان تولید میتواند تا سه هفته طول بکشد، در این مدت سلولها در شرایط از پیش تعریفشده ذخیره میشوند، نظارت میشوند و بر اساس عملکردشان درجهبندی میشوند. تجزیه و تحلیل پیشرفته با استفاده از دادههای درون خطی میتواند به طور قابل توجهی این فرآیند را از طریق شناسایی اولیه سلول های پرخطر کوتاه کند. فقط این سلولها تحت فرآیند پیری کامل قرار می گیرند و زمان پیری سلول های کم خطر را تا 80% کاهش می دهند. این رویکرد با به حداقل رساندن نیاز به فضای ذخیره سازی، هزینههای سرمایهای برای تجهیزات و امکانات را کاهش می دهد. این فناوری در حال حاضر در مرحله افزایش سرعت است.
سیستم عامل از راه دور. تنظیمات کارخانه معمولی به هر دستگاه یک اپراتور اختصاص می دهد. سیستمهای عامل راه دور یک اپراتور را قادر میسازد تا با ارائه دادههای عملیاتی بلادرنگ، مانند ضخامت پوشش و تصاویر زنده، چندین ماشین را مدیریت کند و در عین حال به اپراتور در صورت نیاز به اقدام در یک ماشین خاص هشدار دهد. این رویکرد زمان بیکاری اپراتور را به طور قابل توجهی کاهش میدهد، اما نیاز به یکپارچه سازی از قبل همه تجهیزات با کنترل نظارتی و سیستم جمع آوری داده دارد. این فناوری برای عملیات در مقیاس بزرگ کاملاً بالغ است.
- فرآیندها
بهبود فرآیندهای مهندسی تولید و ساخت، کارایی و ایمنی کلی را افزایش میدهد. اقدامات قابل توجه شامل موارد زیر است.
همکاری OEM. برای اجرای تغییرات عمده در اجزای موسوم به M4 - انسان، ماشین، مواد و روش - تولید کنندگان باتری در حال حاضر به دلیل نیاز به تایید از OEM های خودرو تا 18 ماه زمان نیاز دارند. همکاری نزدیکتر بین OEMها و تولیدکنندگان سلول میتواند این فرآیند را سادهتر کند و امکان بهبود سریعتر کارخانه و مزایای مشترک را فراهم کند.
کل نگهداری مولد. تولید سلول های باتری یک صنعت دارای ارزش افزوده است که به حداکثر رساندن استفاده از تجهیزات برای توزیع هزینه های ثابت بر روی حجمهای بالای تولید بسیار مهم است. کل اقدامات نگهداری و تعمیرات مولد می تواند به حداقل رساندن زمان خرابی کمک کند. یکی از جنبه های حیاتی نگهداری کل تولیدی، تعمیر و نگهداری مستقل است که اپراتورها را قادر میسازد تا مراقبتهای اولیه از تجهیزات را به طور مستقل انجام دهند. این امر اتکا به تیمهای تعمیر و نگهداری اختصاصی را کاهش می دهد و با نگهداری در شرایط بهینه از خراب شدن تجهیزات جلوگیری می کند.
برای اطلاع از آخرین پیشرفتها در حوزه ذخیره سازها الکتریکی همراه ما بمانید.